The pandemic has meant for me a sudden halt in my clinical rotations at the hospital and confinement at home. It was rather frustrating to see the crisis unfold in our healthcare system and especially in our senior’s residences and stand here by the sidelines. However, I soon found a way to partake in this vast effort to fight off Covid-19 by volunteering along with dozens of my peers for the HowITreatCovid19.com project:
Our website is dedicated to helping healthcare professionals find accurate and up-to-date information about the best ways to manage and treat patients affected by the COVID-19 outbreak.
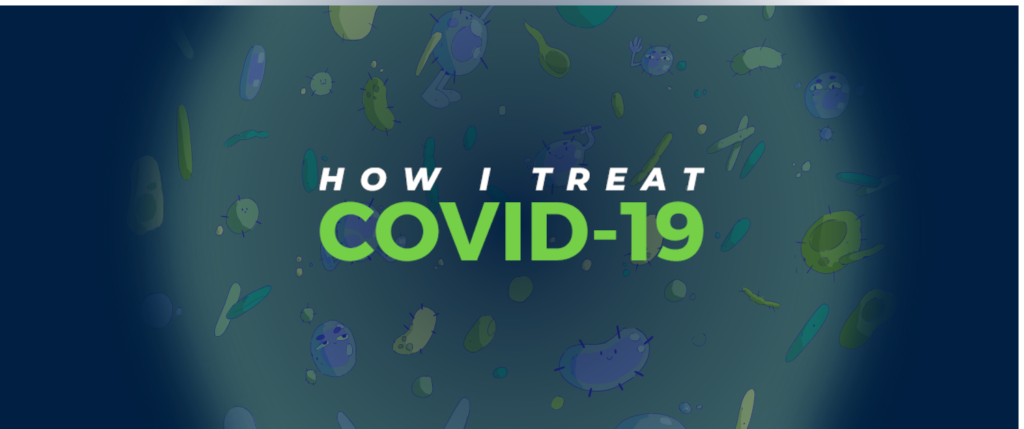
Most other volunteers dedicated themselves to sifting through the vast amounts of scientific publications coming out each day. As for myself, I renewed with my previous job as a web developer and got busy building the platform and some of it’s editorial processes.
Every little bit (of code) truly helps in this fight.